JetBOx™
- General information
- Variations
- Our technology – your advantage
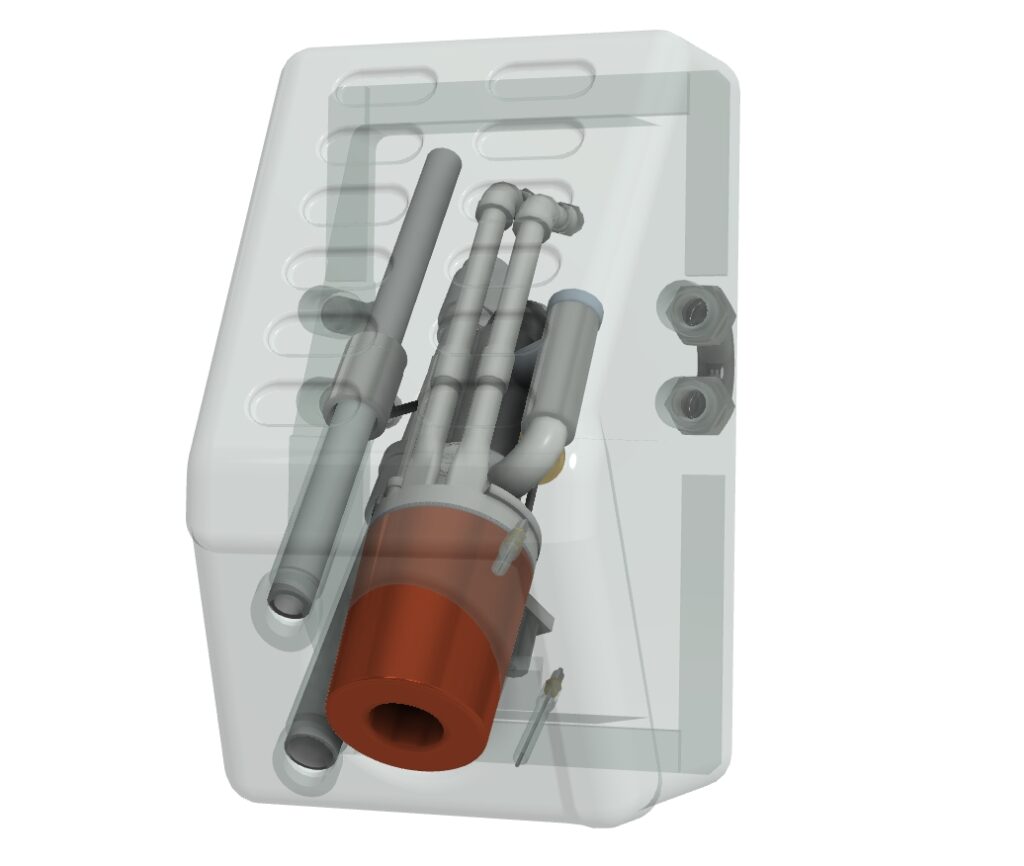
INTECO PTI’s concept has promoted the most aggressive introduction of oxygen and chemical energy into the Electric Arc Furnace (EAF) resulting in dramatic efficiency and utilization improvements. To employ this concept safely, INTECO PTI invented a unique water-cooled copper box (JetBOx™) which houses the burner and injector very low inside the EAF at a steep angle.
The JetBOx™ is designed to position the burner and oxygen injection as close to the steel bath as possible for the highest injection efficiency with no fear of damage to the EAF as it provides excellent cooling protection and is capable of withstanding the impact of falling scrap and splashing of slag and molten metal.
The JetBOxes™ are situated just above the last course of refractory bricks with their front face in line with the hot face of bricks. This location provides several advantages for EAF operations.
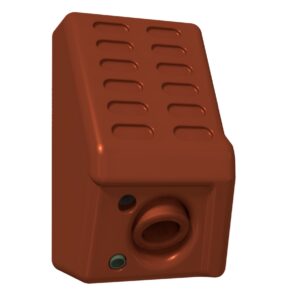
Cast JetBOxTM
standard (35.5x22x20,5“, 1985lbs)
1 or 2 ports at different port position and sizes
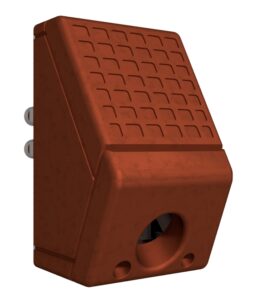
Forged JetBOxTM
standard size
mini Forged JetBOxTM
1 or 2 ports at different port position and sizes
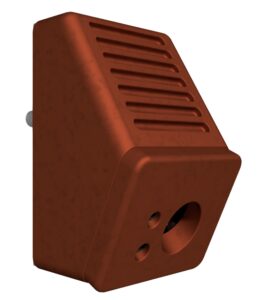
Hybrid JetBOxTM
cast host and machined front face
available in standard size
1 or 2 ports at different port position and sizes
- Enables better energy transfer into the scrap while in melting mode
- Minimizes plugging from splashing slag and molten metal during EAF operation
- Eliminates overheating problems in adjacent panels by moving the burner further from the panels‘ hot face
- Promotes higher oxygen efficiency due to shorter jet length and the ability to use the optimal injection angle
- Allows carbon and lime injection to be applied closer to the molten bath promoting better foamy slag and minimizing material losses
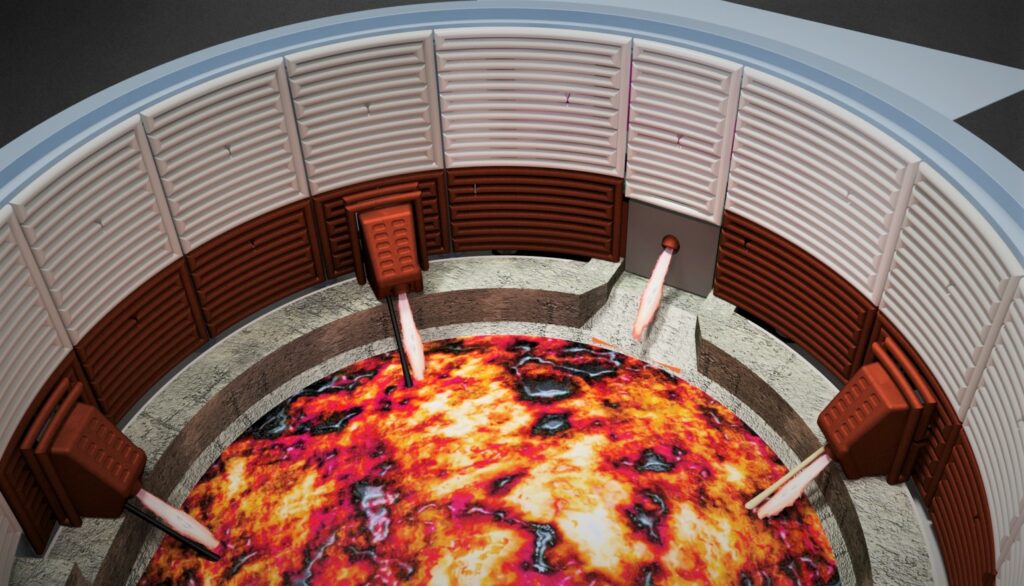
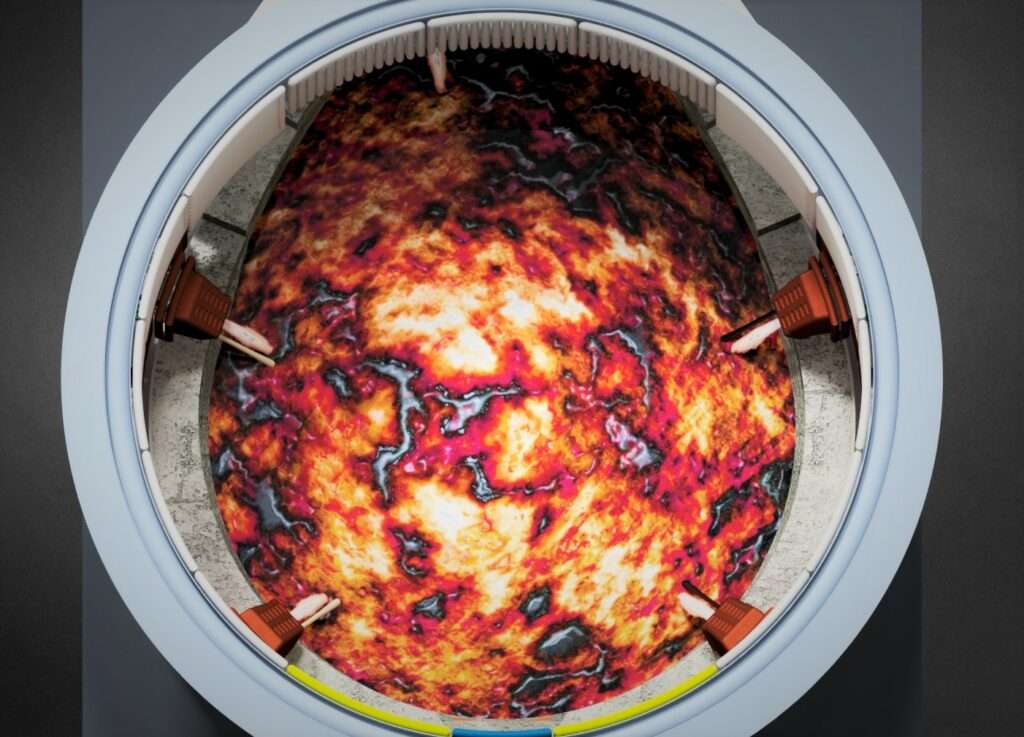
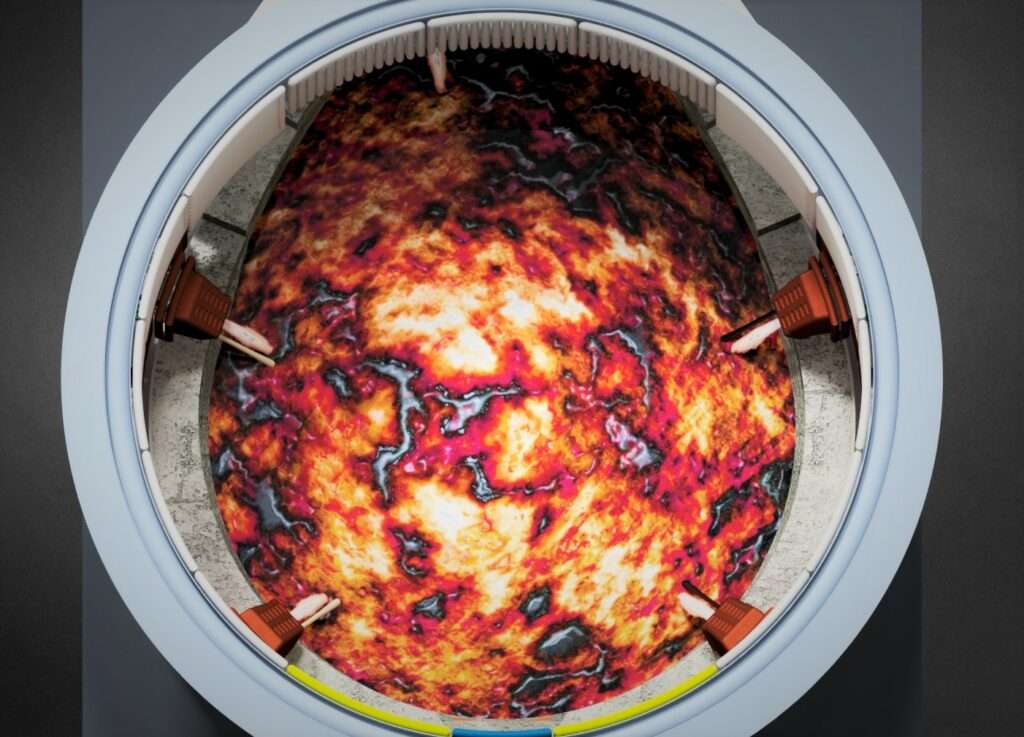
- General information
- Variations
- Our technology – your advantage
INTECO PTI’s concept has promoted the most aggressive introduction of oxygen and chemical energy into the Electric Arc Furnace (EAF) resulting in dramatic efficiency and utilization improvements. To employ this concept safely, INTECO PTI invented a unique water-cooled copper box (JetBOx™) which houses the burner and injector very low inside the EAF at a steep angle.
The JetBOx™ is designed to position the burner and oxygen injection as close to the steel bath as possible for the highest injection efficiency with no fear of damage to the EAF as it provides excellent cooling protection and is capable of withstanding the impact of falling scrap and splashing of slag and molten metal.
The JetBOxes™ are situated just above the last course of refractory bricks with their front face in line with the hot face of bricks. This location provides the several advantages for EAF operations.
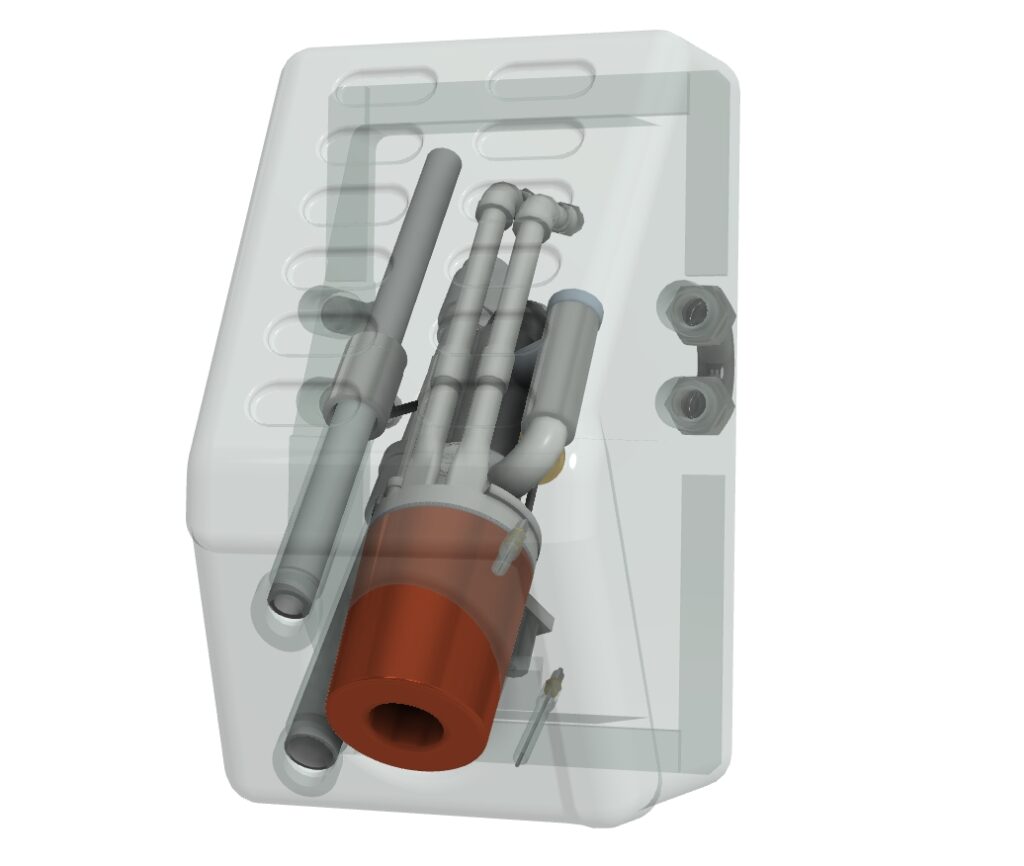
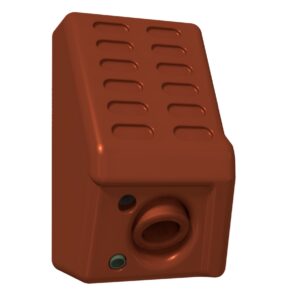
Cast JetBOxTM
standard (35.5x22x20,5“, 1985lbs)
1 or 2 ports at different port position and sizes
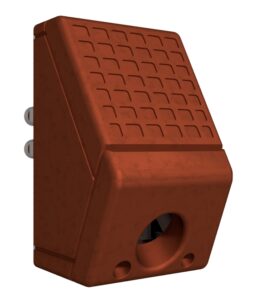
Forged JetBOxTM
standard size
mini Forged JetBOxTM
1 or 2 ports at different port position and sizes
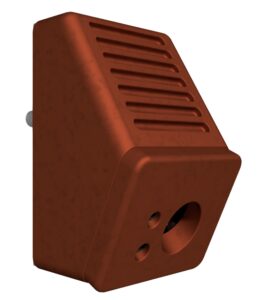
Hybrid JetBOxTM
cast host and machined front face
available in standard size
1 or 2 ports at different port position and sizes
- Enables better energy transfer into the scrap while in melting mode
- Minimizes plugging from splashing slag and molten metal during EAF operation
- Eliminates overheating problems in adjacent panels by moving the burner further from the panels‘ hot face
- Promotes higher oxygen efficiency due to shorter jet length and the ability to use the optimal injection angle
- Allows carbon and lime injection to be applied closer to the molten bath promoting better foamy slag and minimizing material losses