Lime Injection System
- General information
- Our technology – your advantage
Process optimization
INTECO PTI’s lime injection system is designed to balance lime distribution while minimizing lime consumption. By injecting lime directly to the molten bath, the lime dissolves into the slag almost instantly. As a result, the removal of phosphorus occurs earlier in the process. The lime injection system saves you money by reducing lime usage, reducing the amount of housekeeping required in the meltshop, and reducing the amount of lime lost to the baghouse as KO61 hazardous waste.
Closed loop flow control
The lime flow rate is regulated by closed loop control of the vessel pressure and transport air flow. Lime flow is not interrupted by the opening and closing of the cycling lime feed valve. With virtually no moving parts during the injection process, your lime injection system will last longer and require less maintenance. Less lime usage, reduced maintenance and a cleaner shop make the INTECO PTI lime injection system a “no brainer” for your melt shop!
Automated maintenance
The lime injection system is self diagnostic. Features within the vessel help minimize lime plugging and ensure an even and consistent lime flow. Robust and built with quality components, INTECO PTI’s lime injection system will make your lime injection process virtually maintenance free.
Automation
INTECO PTI’s lime injection system is PLC controlled. To fit your needs, the PLC may be mounted directly on the vessel structure or located remotely. INTECO PTI can customize its vessel automation systems to integrate with your current systems to reduce redundant operator displays.
Injection system upgrades
INTECO PTI has made a lot of upgrades to our injection technologies over the years. If you have an older system that is in need of upgrading, we can easily refurbish it with our newest technology package to make it in line with our current equipment in the steel Industry.
Single or dual injection points
Each lime vessel injects material into a single point on the EAF. Most processes need two injection vessels – one vessel for high calcium lime and one vessel for dolo lime. Each vessel has the capabilities to have dual outlets if needed.
- Environmentally clean
- Reduces lime consumption
- Reduces housekeeping problems
- Reduces lime lost to baghouse as KO61 hazardous waste
- Integrates with existing operation systems
- Injects up to 100% of EAF lime needs
- Designed to inject through INTECO PTI‘s JetBOxTM
- Anti-plugging technology delivers continuous lime
Lime Injection System
- General information
- Our technology – your advantage
Automated maintenance
The carbon injection system is self diagnostic and self adjusting. Features within the vessel help minimize carbon port plugging and ensure an even and consistent carbon flow. The carbon injection system has a self-diagnostic system that monitors the carbon flow along with critical system parameters. A robust design with high quality components, the carbon injection system will make carbon injection to any EAF virtually headache free.
Process optimization
INTECO PTI’s carbon injection system is designed to balance carbon distribution while minimizing carbon consumption. By injecting carbon to multiple points within the EAF, it provides a more consistent, foamy slag and a more homogenous steel bath. Since the carbon injection system is fully automatic, it frees up valuable operator time to concentrate on steelmaking.
Injection system upgrades
INTECO PTI has made a lot of upgrades to our injection technologies over the years. If you have an older system that is in need of upgrading, we can easily refurbish it with our newest technology package to make it in line with our current equipment in the steel Industry.
Automation
INTECO PTI’s carbon system is PLC controlled. To fit your needs, the PLC may be mounted directly on the vessel structure, or located remotely. INTECO PTI can customize its vessel automation systems to integrate with your current systems in order to reduce redundant control interfaces.
Closed loop flow control
A closed loop control of the vessel pressure and transport air flow regulates the carbon flow rate. The opening and closing of a cycling, carbon feed valve does not interrupt the carbon flow. With virtually no moving parts during the injection process, the carbon system lasts longer and requires less maintenance. Additionally, less floor space, fewer vessels and reduced maintenance make the INTECO PTI carbon injection system a “no brainer“ for any melt shop!
Multiple injection points via INTECO PTI‘s new rotary feed technology
The carbon injection system can be customized for up to 3 injection points, all from a single vessel. With fewer vessels required, it saves floor space and money! Single and dual outlets are also available in traditional pneumatic conveying method with knife gates if there is no need for a rotary.
- Environmentally clean
- Reduces lime consumption
- Reduces housekeeping problems
- Reduces lime lost to baghouse as KO61 hazardous waste
- Integrates with existing operation systems
- Injects up to 100% of EAF lime needs
- Designed to inject through INTECO PTI‘s JetBOxTM
- Anti-plugging technology delivers continuous lime
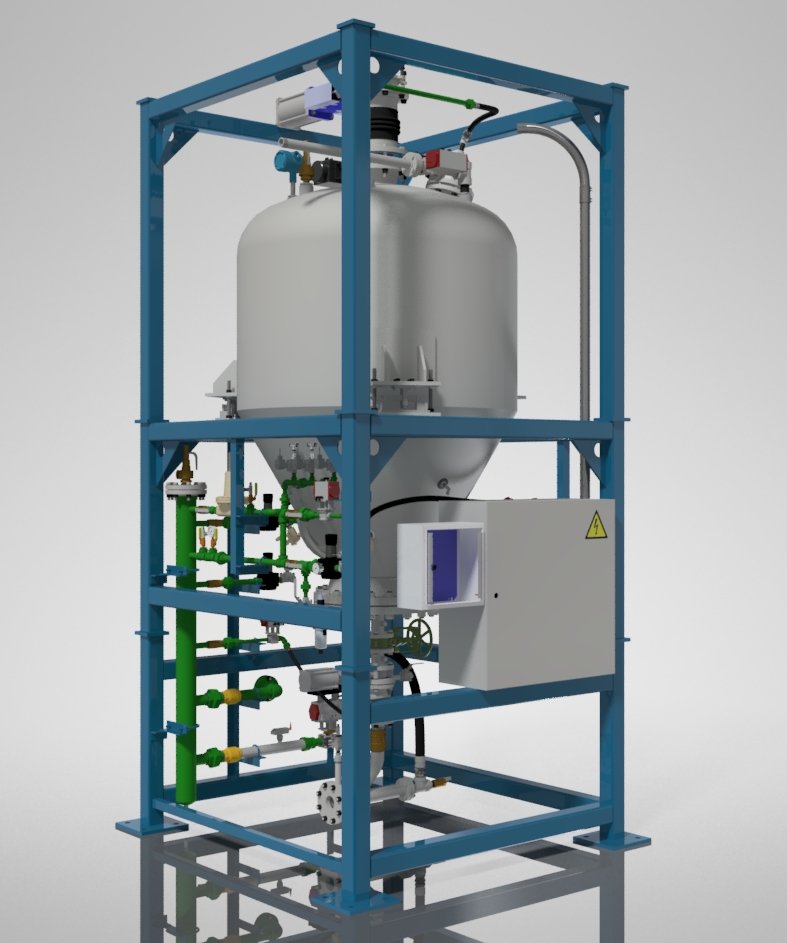
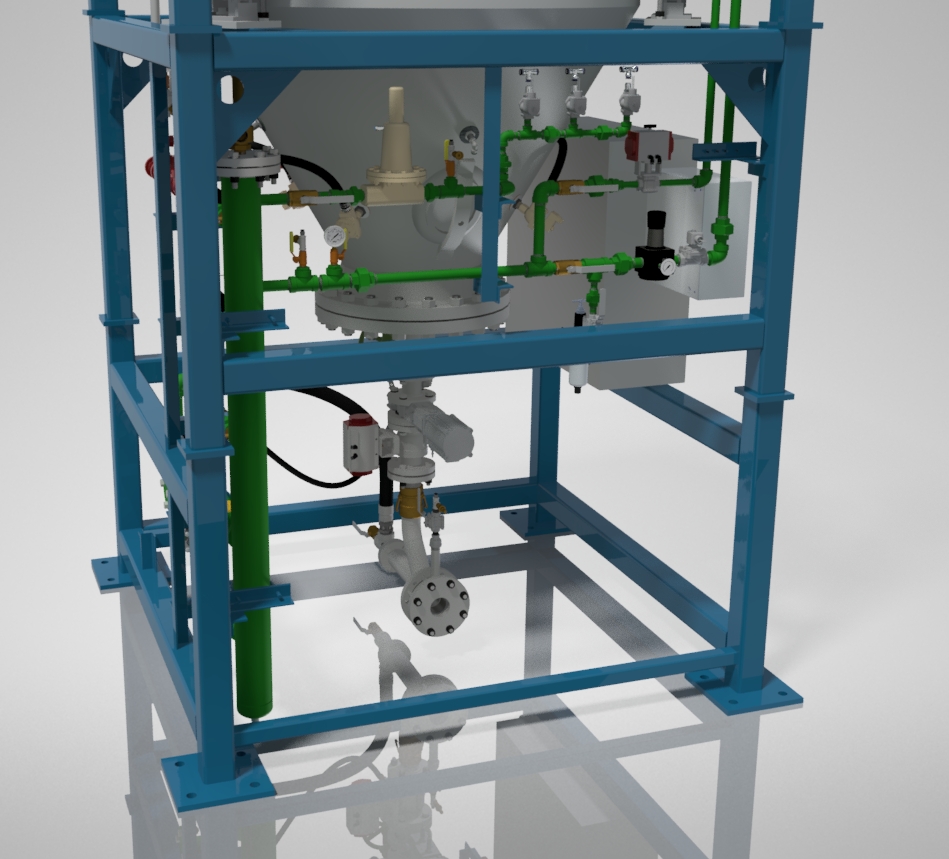