SwingDoor
- General information
- Requirements for implementation
- Our technology – your advantage
The INTECO PTI SwingDoorTM is designed for modern EAF operation. The system is specifically made to allow the EAF to operate with a closed slag door which notably improves operator safety. The position of the SwingDoorTM prevents scrap from accumulating in the slag door area and furnace breast. The new system does not require the slag door area to be cleaned during the EAF melting cycle. It is designed to maintain a thick layer of slag in the furnace. This improves arc efficiency and reduces energy and additive consumption by allowing the operator to the control slag level in the furnace during the whole melting time.
The INTECO PTI SwingDoorTM is mounted flush with the hot face of the water-cooled panels. By installing the SwingDoorTM in-line with the water-cooled panels, the slag door tunnel is eliminated and scrap is prevented from accumulating on the furnace breast. The SwingDoor‘sTM integrated burner operates with the same efficiency as a sidewall burner due to its proximity to the scrap and steep burner angle. The combination of the closed door and the integrated burner stops slag and steel from building up in the breast area. As a result, the slag door area is automatically cleaned and the need for a slag door lance or mechanical pusher is eliminated.
Hydraulic drive: Double actuator for 120° swing, 110 l/min flow at nominally 150 bar hydraulic fluid pressure ( higher pressure can be used to fit to the overall EAF system pressure). Avaliable torque – up to 67 00 Nm.
Cooling Water: 0.5 m³/min minimum cooling water flow rate at 2 bar(g) min. Δp
- Avoids furnace door tunnel
- Charging and melting with door closed
- No scrap falling to EAF breast
- Self clearing feature with integrated burner – no scrap
pushing from the door - Controlled deslagging – stops slag flow by door closing
- Up to 1m consistent slag layer in the furnace
- Improved yield and energy use
- Increases yield average 0.8%-1% (impact translates to ≈ 5 kWh/t+)
- Decreases energy consumption up to 10 kWh/t
- Decreases electrode consumption 0.5 lbs/t
- Direct and indirect CO2 savings of combined 16.5 lbs CO2 per ton of liquid steel produced
- Reliable robust design – low maintenance
- Easy installation for any furnace shell
- Fast payback
- Main purpose: Operator safety
SwingDoor
- General information
- Requirements for implementation
- Our technology – your advantage
The INTECO PTI SwingDoorTM is designed for modern EAF operation. The system is specifically made to allow the EAF to operate with a closed slag door which notably improves operator safety. The position of the SwingDoorTM prevents scrap from accumulating in the slag door area and furnace breast. The new system does not require the slag door area to be cleaned during the EAF melting cycle. It is designed to maintain a thick layer of slag in the furnace. This improves arc efficiency and reduces energy and additive consumption by allowing the operator to the control slag level in the furnace during the whole melting time.
The INTECO PTI SwingDoorTM is mounted flush with the hot face of the water-cooled panels. By installing the SwingDoorTM in-line with the water-cooled panels, the slag door tunnel is eliminated and scrap is prevented from accumulating on the furnace breast. The SwingDoor‘sTM integrated burner operates with the same efficiency as a sidewall burner due to its proximity to the scrap and steep burner angle. The combination of the closed door and the integrated burner stops slag and steel from building up in the breast area. As a result, the slag door area is automatically cleaned and the need for a slag door lance or mechanical pusher is eliminated.
Hydraulic drive: Double actuator for 120° swing, 110 l/min flow at nominally 150 bar hydraulic fluid pressure ( higher pressure can be used to fit to the overall EAF system pressure). Avaliable torque – up to 67 00 Nm.
Cooling Water: 0.5 m³/min minimum cooling water flow rate at 2 bar(g) min. Δp
- Avoids furnace door tunnel
- Charging and melting with door closed
- No scrap falling to EAF breast
- Self clearing feature with integrated burner – no scrap
pushing from the door - Controlled deslagging – stops slag flow by door closing
- Up to 1m consistent slag layer in the furnace
- Improved yield and energy use
- Increases yield average 0.8%-1% (impact translates to ≈ 5 kWh/t+)
- Decreases energy consumption up to 10 kWh/t
- Decreases electrode consumption 0.5 lbs/t
- Direct and indirect CO2 savings of combined 16.5 lbs CO2 per ton of liquid steel produced
- Reliable robust design – low maintenance
- Easy installation for any furnace shell
- Fast payback
- Main purpose: Operator safety
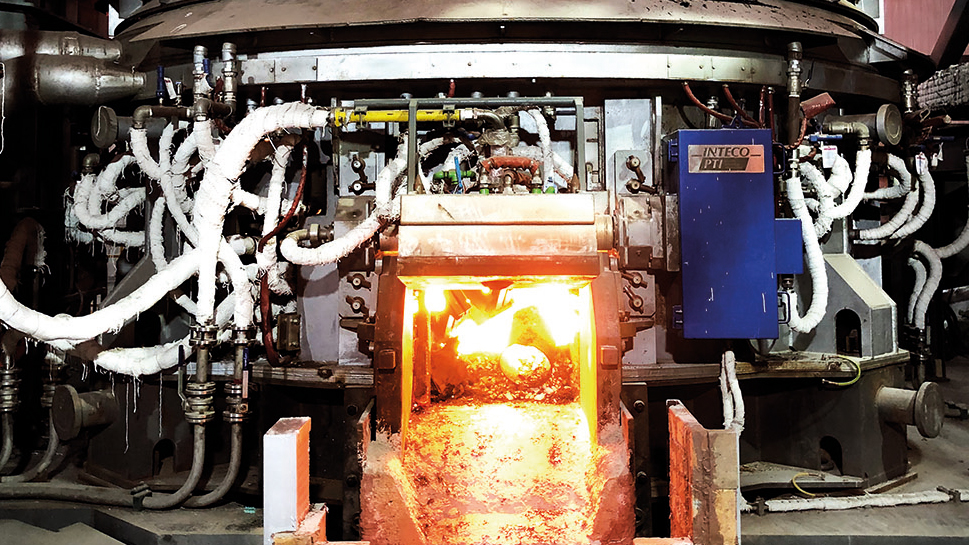
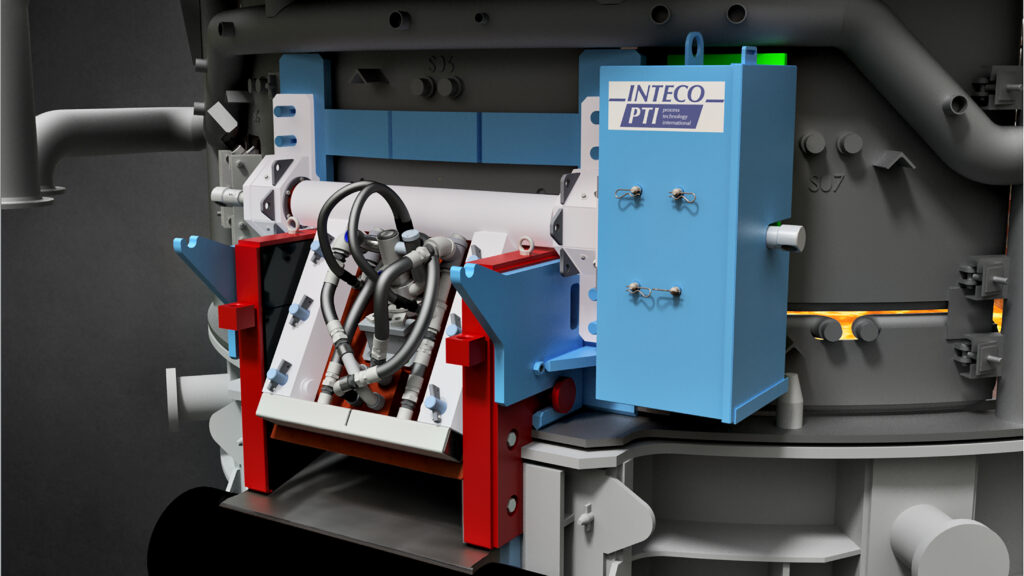
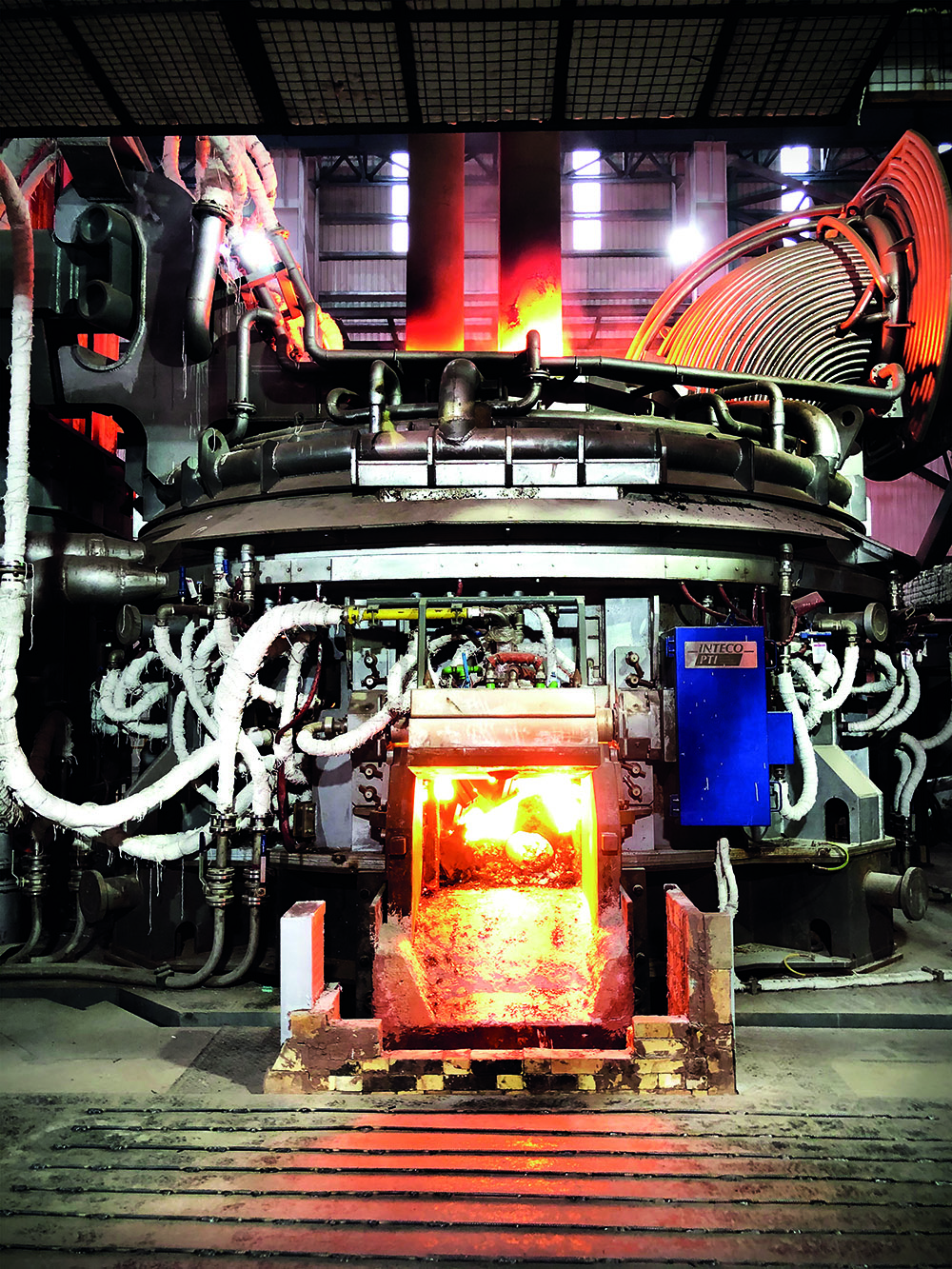
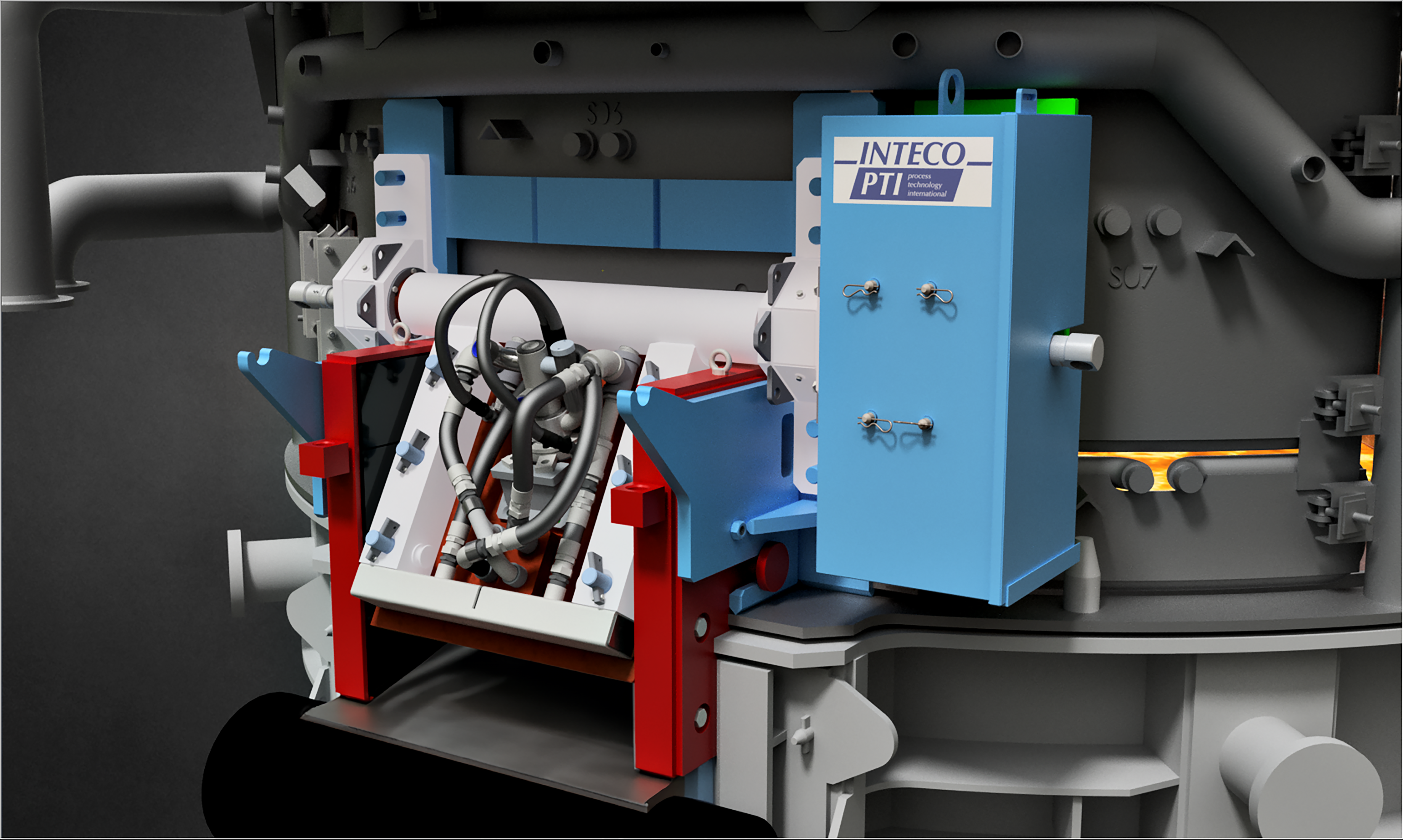